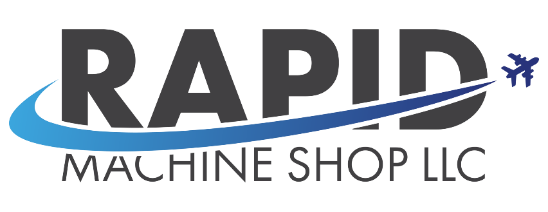
Applied Innovation
General Aviation Gets a Boost from Winglets Built by Rapid Machine Shop, Wichita, Kansas
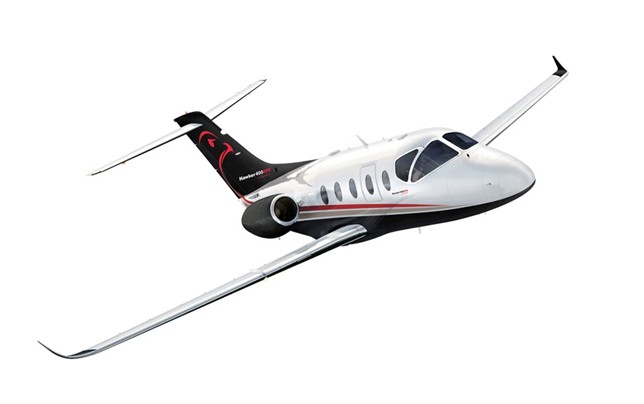
Rapid manufacturing processes produce aftermarket winglets, providing benefits to general aviation aircraft. Hawker 400XPR is shown.
Winglets are vertical extensions attached to wing tips to reduce aerodynamic drag without increasing wingspan.
Winglets were first used on general recreational aircraft in 1975 when Burt Rutan introduced them on the Rutan VariEze. In 1977, Learjet Corporation incorporated winglets on its prototype Learjet 28 and later became the first production jet to use them to optimize efficiency.
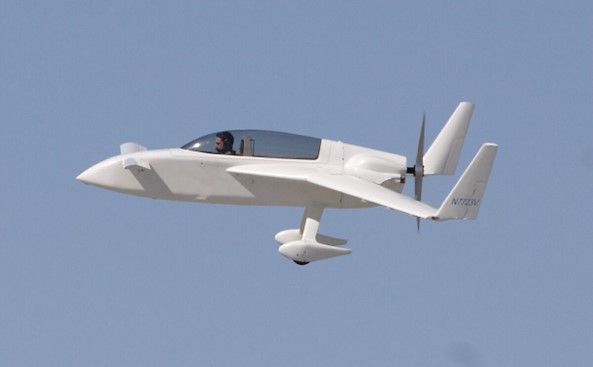
Rutan VariEze developed in 1975
Winglets promise to reduce the strength of the vortex coming from the tip of the wing, which allows the flow across the wing to be more two-dimensional. During the 1970s and 1980s, Flight tests conducted by NASA found a 6.5% reduction in the fuel use of a Boeing 707-type airliner when using winglets. The design of winglets has continued to evolve, realizing additional operational benefits, including flight speed increases, noise reduction, reduced takeoff and landing distance, and a shorter overall wing length required, which makes moving around airport tarmacs easier. Winglets add weight and aren’t as efficient as a longer wing. It’s estimated that winglets are about 2/3 as efficient as making the wing longer. However, winglets can keep the wingspan short and do not place significant additional load on the spar.
Improving a Legacy Platform
Many small Jets have stood the test of time and are popular platforms for private business and personal travel. The Hawker 400XP, for example, was initially manufactured between 1978 and 2009. It has a maximum range of 1534 miles and a maximum speed of 518 mph.
Driven by strong customer demand for factory-engineered and supported upgrades to the Hawker 400XP, the company completed extensive aerodynamic, propulsion, and system studies in 2010. The objective was to establish the performance and features of the next-generation Hawker 400XP.
The result was the Hawker 400XPR performance upgrade package. The upgrades set a new factory standard in the light jet market for performance, reliability, cabin size, and range at an affordable price point. The Hawker performance upgrade package included new engines and upgraded avionics, but the most significant contributor to the latest performance specs was the addition of winglets.
The upgraded HawkerXPR has superior hot/high airfield performance, climbs direct to maximum altitude, flies over 1,950 transcontinental nautical miles, and delivers outstanding flexibility while costing significantly less to operate than non-upgraded Hawker 400XP series aircraft.
Hawker 400XPR Aerodynamics
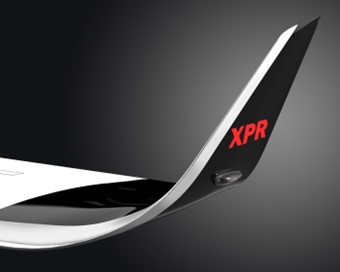
HawkerXPR winglet
In the case of the Hawker 400XPR, adding winglets increased the wing’s aspect ratio to diminish lift-induced drag effectively. Benefits include reduced fuel consumption, improved time-to-climb performance, faster cruise speeds, and increased range. Hawker Winglets also improve low-speed and high-altitude handling characteristics by enhancing stabilization in flight, not to mention excellent ramp appeal. LED position lights are incorporated into the winglet design and are projected to have a Mean Time Between Failure (MTBF) of 5,000 hours.
Building General Aviation Winglets
Rapid Machine Shop LLC (RMS), Wichita, Kansas, manufactures aftermarket winglets for general aviation applications. Nohemy Martinez, President, started the precision aerospace parts manufacturing company in 2002, which has grown year-over-year based on its reputation for delivering high-quality parts on time and within budget. RMS specializes in producing challenging parts for aerospace, spaceflight, and national defense applications. Quality verification and reporting are priorities for every job undertaken by RMS. Each part is assigned a master shop traveler packet for process traceability and transparency. RMS is AS 9100D and ISO 9001:2015 certified.
RMS builds winglets from beginning to end, including chemical treating and priming. Finished winglets are color-matched as part of the final installation process. RMS has the complete range of experience, technology, and equipment to handle the job, including CAD/CAM software, reverse engineering software, portable CMMs for tool building, fixture design, and final quality inspection. Expert welding, press break, rubber block forming press, and multi-axis CNC machines support precision forming operations.
Winglets are not merely affixed to the wing tips but wholly integrated. Given their location compared to the rotational center of the aircraft, any disturbance caused by a deviation from the nominal will be amplified. From the material to comparable metal bend and spring back allowances to the functional and esthetic design characteristics, winglets are meticulously designed and engineered to tight tolerances. To support production, the manufacturing process must conform to the specifications and deliver traceability and documentation across all drawings, models, programs, fixtures, materials, and tools. Certificates of conformance, materials, outside processing, and a final inspection report accompany every finished part shipped.
Rubber Pad Forming Fabrication
Typical metal forming and fabrication do not usually require tight tolerances, but precision is essential when dealing with a foil at the bitter end of a wing. Several components comprise a finished winglet to ensure desired airflow, structural integrity, continuity with the designed taper, and wing flexibility. The upper winglet (and, in some designs, a smaller lower winglet) is responsible for redirecting airflow and must adhere to tight tolerances. Precision forming, fabrication, and quality verification must be applied throughout the build process. Complex surface profiles are achieved through rubber pad forming with allowances for predicted metal bend and spring back using 6061 aluminum sheet material.
Build Process Guided by Metrology Solution
To help reverse engineer complex surface profiles and components, design and build tooling, and verify quality, traceability, and reporting associated with each winglet manufactured, RMS uses a Master3DGage portable CMM powered by Verisurf software. The complete hardware/software solution delivers automated ‘in-process’ reverse engineering and inspection in a model-based CAD/CAM environment on the shop floor. Typically, RMS works from customer-supplied intelligent CAD models. Still, if reverse engineering is required, for example, to capture a missing feature, measurement data of prismatic geometry or complex surfaces are captured using contact probing or contactless 3D digital scanning with a hot-swappable scanner option.
Importing CAD Model
Once the winglet design is complete and the CAD/CAM model is approved, RMS uses Verisurf software to guide the build process. With the Verisurf Model-Based Definition (MBD) process, the original 3D model, not a secondary drawing, is the authority dataset against which all manufacturing is verified. To ensure critical data is not lost or altered when the intelligent model moves into Verisurf, the completed import is analyzed with Verisurf Validate software to confirm the integrity of the data against the source file.
Tooling
Verisurf software is built on top of the Mastercam platform. This enables interoperability between Verisurf and Mastercam’s CAD/CAM functionality. Using the Master3DGage and Verisurf Reverse software, the nominal CAD model of the winglet is used to reverse engineer a precision mold tool (form block) to mold complex surfaces.
The CAM file for the newly created mold tool is used to mill a precision aluminum form block. Using the Master3DGage, the finished block is inspected for any deviation from the nominal and confirmed to be within specified tolerances.
Rubber Pad Forming
The form block is placed in a hydro-press with an aluminum blank placed between the form block and a series of rubber pads made of hard urethane. Four thousand pounds of direct pressure is applied to form the part over the form block. All formed components are inspected and verified against the nominal CAD model to ensure acceptable tolerances are met.
Final Assembly and Inspection
Following the final assembly of each winglet, the finished part undergoes a complete visual and metrology profile inspection using Master3DGage. Approved parts go through chemical etching, and primer is applied before being shipped for installation. Final color matching is done as part of the installation process.
Maintenance Repair and Overhaul (MRO)
Metrology tools and applications have improved the overall quality, fit, and finish of many MRO challenges. Fabricating winglets is an example of adding efficiency to an existing platform. A similar development and manufacturing process can be applied to legacy aircraft parts that are no longer supported or available. The ability to design bespoke replacement parts or develop and integrate new ideas to a proven platform is a real and present option for today’s aircraft MRO.