AI Insight:
Understanding First Article Inspection in Manufacturing
TL;DR: First Article Inspection (FAI) ensures that manufactured parts meet design specs from the start. Verisurf simplifies the process with CAD-based workflows and automated reporting.
What is First Article Inspection
First Article Inspection (FAI) is a manufacturing and quality assurance process to satisfy product specifications and quality requirements before full production begins. It typically involves a detailed examination of the first sample produced from a manufacturing run, known as the “first article.” This inspection is critical in scenarios such as:
- Introduction of a New Product: When a new product is manufactured for the first time.
- Change in Design or Process: Whenever there are significant changes to the design or manufacturing process of an existing product.
- Transfer of Production: When production is transferred to or from a different manufacturing facility.
Purpose of First Article Inspection
- Verify that the manufacturing process can produce components that meet requirements consistently.
- Ensure that any changes are correctly implemented and have the desired effect.
- Identify any issues early in the production process to avoid costly corrections later.
First Article Inspection Process
The inspection process includes checking the product’s dimensions, material, appearance, and all features against the design specifications. The process compares the product to drawings, parts lists, and other documentation. The inspection results are documented in a First Article Inspection Report (FAIR), which is reviewed and approved before proceeding with full-scale production.
Industry Use of First Article Inspection
FAI is crucial in various industrial quality management systems and standards, such as ISO 9001, AS9100 for aerospace, PPAP for automotive industry standards, and ISO 13485 for medical devices. It acts as a form of risk mitigation, as it helps catch potential issues before production.
Advances In First Article Inspection
Although FAI addresses many aspects of product design and manufacture, dimensional inspection is the most significant. Three-dimensional first-article inspections are primarily performed with coordinate measuring technologies such as stationary, programmable CMMs (coordinate measuring machines), portable CMM arms, and non-contact scanners. Historically, two-dimensional measurements are made with hand gages such as micrometers, calipers, and height gages; however, CMM inspection has many benefits over traditional hand tools, including higher productivity, consistency, accuracy, and improved process control. In addition, advances in 3D CAD/CAM models have replaced blueprint drawings, sparking the modern “digital product definition” (DPD) age, making first article inspection via CMM technology and DPD a very productive pairing.
FAI Adopters – Aerospace, Automotive, and Medical Industries
The term “first article inspection” applies to a standard operating procedure used in the aviation, space, and defense industries, and is defined by SAE specification AS9102 Aerospace First Article Inspection Requirement, written and controlled by the International Aerospace Quality Group (IAQG).
For the automotive industry, the Production Part Approval Process (PPAP), defined in detail by the Automotive Industry Action Group (AIAG), is the well-established practice of inspecting products for design and manufacturing verification in the early stages of production. First article inspection is part of PPAP or may precede full-blown PPAP. The difference is that FAI is conducted on the first part or parts produced from a new or changed design, and PPAP is a more extensive process evaluating a series of parts from a full production run for new parts.
The medical products industry requires manufacturers to put FAI or something comparable to FAI into practice by requiring a process that verifies product compliance with ISO 13485 Medical Devices – Quality Management Systems specification.
Aerospace – First Article Inspection Requirement – the AS9102
First article inspection (FAI) per AS9102 is an established process and requirement for aviation, space, and defense manufacturing sub-contracts. Having been proven and refined over many years, it has also become a reliable best practice for other industries. FAI is enforced as a contractual requirement dictated by strict conformance to the SAE AS9102 specification, mandated to ensure fully verified and documented quality as a new product begins manufacturing. Safety of flight issues present the primary need for such diligence and adherence to a controlled process. Furthermore, consistency across a widely distributed supply chain with methodology that is scalable and reliable must be proven to be achievable by all stakeholders.
The AS9102 details the full scope of activity and documentation required, even establishing a set of forms that ensure all aspects of design, DPD, manufacturing, materials, engineered processes, testing, and inspection are verified and recorded so that nothing gets overlooked. Dimensional inspection typically requires the most time and effort of all the FAI tasks. While digital definition is an advancement for improving productivity throughout the product lifecycle, it has created the need for additional controls to be added into the FAI process to ensure accuracy and consistency as well as conformity across the supply chain. The “digital thread” must stay intact, and controls are required to prevent errors, especially when handing off digital information from one platform to the next. Appropriately, the AS9102 specification has been updated to include the necessary controls.
In more recent times, the aerospace industry has begun to introduce its supplier base to automotive industry-style PPAP requirements. This can be seen in aerospace standard AS/EN/JISQ 9145:2016 from the IAQG and confirmed by Boeing X38656 for Advanced Product Quality Planning (APQP) and Production Part Approval Processs (PPAP).
Automotive – PPAP – Production Part Approval Process
The purpose of PPAP is to determine if all customer engineering design and specification requirements are properly understood by the supplier and that it yields products consistently meeting the requirements during an actual production run at the quoted production rate. Furthermore, it validates more than just the part, but also the entire engineering, manufacturing, supply chain, and quality control aspects of the product lifecycle. What’s similar between FAI and PPAP is both require full dimensional inspection and reporting (among other requirements).
FAI-type inspection is a part of the PPAP but differs from aerospace due to the unique nature of automotive manufacturing, produced at much higher volumes, differing government regulations, aesthetics of part surfaces, legacy industry methodology and expectations, and more. With eighteen elements identified in the PPAP framework, the quality control plan, measurement system analysis, and dimensional results are among the drivers that lead manufacturers to a similar dimensional inspection process.
Medical – Quality Management Systems – ISO 13485 for Medical Devices
First article inspection (FAI) is a necessary step to ensure a manufacturing process will create a medical device that works as designed and meets requirements. The data and measurements gathered from FAI become part of the medical device file, which is required for FDA submissions and ISO 13485 compliance. Even though ISO 13485 is a stand-alone standard, it is based on ISO 9001. So, while ISO 9001 is an internationally recognized standard for any organization in any industry, the ISO 13485 standard includes added requirements that are specific for companies that manufacture ISO-compliant medical devices.
Planning for FAI
As part of an organization’s quality management system (QMS), manufacturers adhering to ISO standards need an overall quality plan to monitor and control all aspects of part production and an inspection plan that focuses on measurement throughout the product lifecycle. The AS9102 specification requires them to have an FAI plan that is specific to new production runs. As a sub-contract requirement, source inspectors want to see that their suppliers are not just checking parts, but have a documented process for inspection, management of non-conformances, and corrective actions when necessary. The inspection plan is based on the technical data package tied to the customer contract. The manufacturer’s QC department uses drawings, material and process specifications, bill of materials (BOM), digital datasets such as CAD, and other sources from which to create the inspection plan. The manufacturer must follow and document all DPD protocols (for example, ASME Y14.41 & Boeing D6-51991 specifications) to ensure there is no disconnect within the product definition exchange to prevent incorrect or superseded data from being used erroneously.
The manufacturer’s QMS establishes the policies and workflows for their inspectors to ensure compliance with the appropriate standards. Compliance auditors will verify that the quality manual and FAI procedures are followed and meet the applicable requirements.
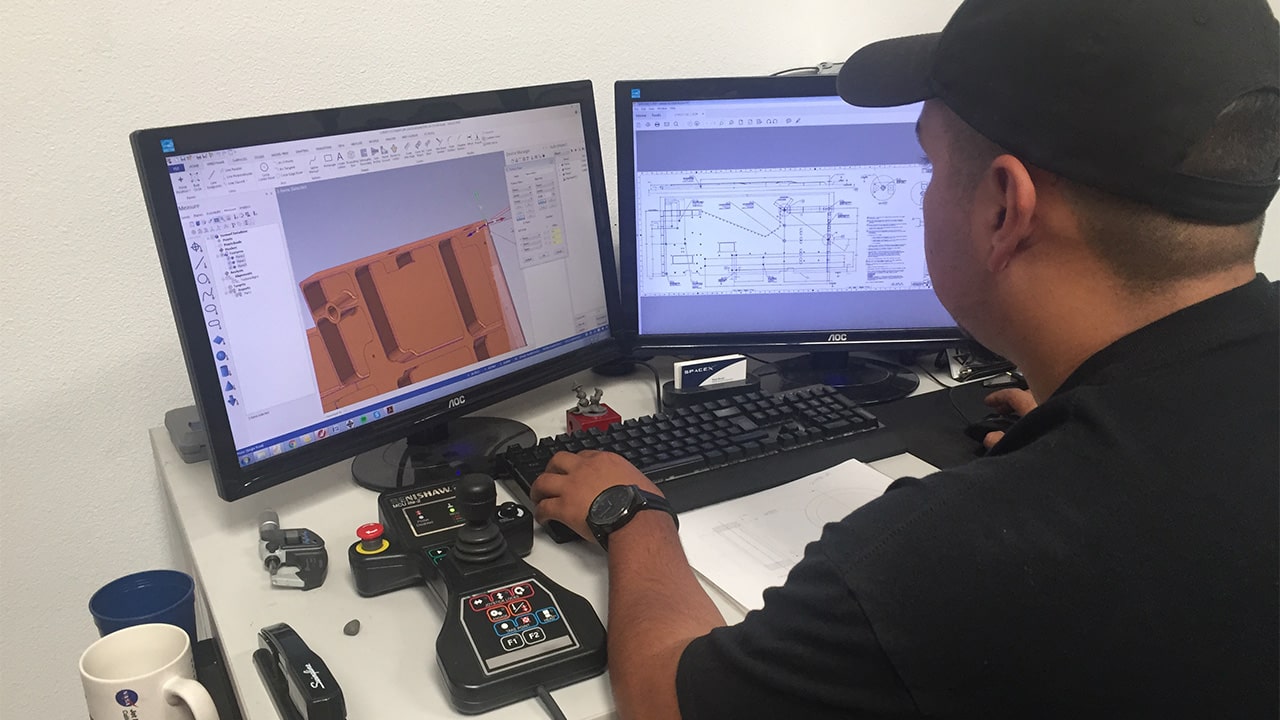
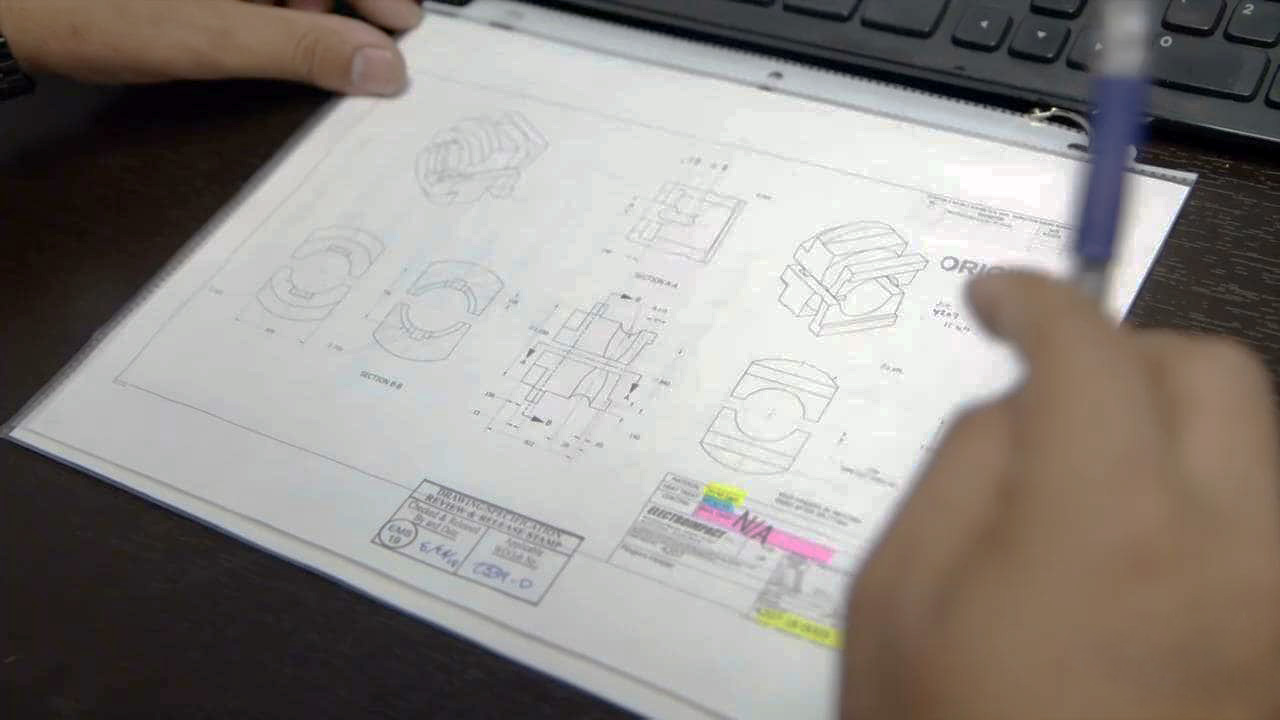
First Article Inspection Report (FAIR)
To make sure that all important characteristics are verified, there must be no disputing what the baseline (nominals) and tolerances for those characteristics are. What is acceptable or not acceptable, must be clear. Therefore thorough and traceable documentation is necessary and is the main purpose of the first article inspection report (FAIR). It is both the sub-contract deliverable as well as the historical record, which can serve a number of purposes down the road.
Included in a complete FAI is an accounting of all manufacturing processes and equipment involved in manufacturing, planning, procurement, sub-contracting, and quality assurance of the product. It requires confirmation of equipment maintenance (such as machine calibration and certification), bill of materials, chemistry, heat treatment, surface finish, material certifications, material properties, and purchased parts. The AS9102 specification establishes a standardized format ensuring that the FAI process is complete and that the foundation is set for apples-to-apples comparisons between successive parts.
The AS9102 standard requires three forms to be included in the FAIR:
Form 1 – Part Number Accountability
Form 2 – Product Accountability – Materials, Special Processes, and Functional Testing
Form 3 – Characteristic Accountability, Verification, and Compatibility
With the primary focus of this article being dimensional inspection; we will concentrate on Form 3 in what follows.
Form 3: Characteristic Accountability Verification and Compatibility Evaluation
The AS 9102 Form 3 is the record of characteristics measurements alongside associated design values and tolerances in a line-by-line chart form. Each record also notes the characteristic’s either conforming or non-conforming condition. For the most part, all drawing dimensions and specified requirements are included. Each characteristic gets its own line labeled with an ID number (some line items report on a group of features when necessary). Line items from Form 3 coincide with characteristics noted on the engineering drawing or DPD with a circled “balloon” ID number. This is from where the term “ballooned drawing” or “bubble drawing” often referred to by those involved comes from.
In the ballooning process, inspectors create the sequential encircled numbers on the drawing next to each dimension or GD&T callout. The importance of Form 3 must be embraced, and each measurement or observation should be clear and unmistakable. Each design characteristic needs to be easily understood, tolerances or allowable conditions should be clearly noted, non-conformances should stand out on the page, and the values showing the degree of in or out of compliance must be shown.
When the available product engineering is a completely CAD-model-based, digital definition, ID balloons may reside within the model where they can be associated with features. GD&T that is connected to the entity for which it controls, and is usable by the measurement software, is referred to as “associative” or “semantic.” Measurement software such as Verisurf offers associative/semantic GD&T, thereby preserving the digital thread. (see Verisurf MBD – model-based definition)
Form 3 fields and column headers are differentiated by typeface style (bold, bold italic, or standard font) as either required, conditionally required, or optional:
(R) – Required: This is mandatory information. NOTE: These fields are depicted in bold font.
(CR) Conditionally Required – This field shall be completed when applicable to the product (e.g., serial number shall be entered when there is a serial number) or when required by the customer. NOTE: These fields are depicted in bold italic font.
(O) Optional – This field is provided for convenience; the field may be left blank. NOTE: These fields are depicted in standard font.
The Dimensional Inspection
First article Form 3 inspection mostly involves dimensional measuring. (There may also be some design notes and quality process notations that need to be observed and reported as well.) The engineering drawing or DPD model dimensions have an associated tolerance connected to each dimension or GD&T callout/control frame. In some cases, tolerances are controlled by the number of decimal places shown on dimensions which in turn correspond with the tolerances noted in the drawing title block key for each number of decimal places. In effect, the FAI requires that every dimension and callout be measured, recorded, and compared to the nominals (as-designed values). GD&T control frames, per ANSI specification Y14.5, dictate the feature relationship constraints that are to be measured and reported.
For this important step of the FAI, the inspector measures, calculates per GD&T guidelines, and reports each value on Form 3. On each row of the spreadsheet, design values and tolerances are recorded in column 8 “Requirement,” measured values are recorded in column 9 “Results,” and “Pass” or “Fail” noted when applicable. (In some cases that do not involve measured values, reference to the statement of conformance and indication of pass/fail or “accept” may be all that is recorded.) If there are any that fail, a non-conformance number is assigned in column 11. The FAI would be identified as “not complete” and so noted on Form 1 until the issues are corrected and the FAI or partial FAI is completed with no non-conformances.
Generally, measurements are to be recorded as individual values for each characteristic. However, if a group of measurements is identified in the requirements such as callouts for surface profile or hole position, the minimum and maximum may be reported as long as all measurements are within tolerance. If any are out of compliance, the measurements that are non-conforming need to be singled out individually on their own line. For positional tolerance, CMM measured nominal and measured point values are not sufficient, and the actual positional nominal, tolerance, and deviation need to be reported.
![]() | ![]() |
Automating First Article Inspection Ballooned Drawing Reporting
FAI measurement, recording, and reporting by hand is a tedious process, but several first article inspection software offerings, such as SOLIDWORKS Inspection, have been developed to automate the process. These products use optical character recognition (OCR) to read drawing dimensions and GD&T, and automatically add sequenced balloon IDs to each. This data is formatted to a spreadsheet which can be printed, output to a shareable file, or fed into a database for SPC and subcontract management. The complete digital process reduces transcription errors and improves productivity while supporting the digital thread. While inspection using hand tools and manual gages still plays a big role in FAI, modern CMM technology helps to achieve accurate, digitally recorded measurements often in less time than it might take just for the setup for a complex GD&T measurement using manual methods. Inspection with a CNC or DCC, motor-driven CMM is automated by simple, intuitive selection of features and path editing in the CMM software.
Productivity gains can also be achieved by using manual CMM devices such as portable articulating arms controlled by automated, software-prompted program plans. The efficient, digital workflow modernized by applications such as Verisurf software, provides automatic program path creation that streamlines the process even further.
Regardless, automation through either motor-driven CMMs or software-prompted manual CMMs provides productivity enhancements and improved process control over ad hoc, old-school, manual gage measuring.
First Article Inspection Verisurf SolidWorks Inspection Integration
VIDEO (click below)
Gaining Source Inspector Buy-Off
A major goal of all suppliers is to get source inspectors to buy off first articles so their organization can get on with production and make a profit. Furthermore, you want source inspector visits to go as smoothly as possible to strengthen the company’s reputation and opportunities to get more contracts. Automation of the FAI and CMM inspection will impress source inspectors, while a manually performed and handwritten report might make them wonder if the vendor is committed to modern quality processes.
The supplier’s FAI process itself needs to be well-documented and controlled to ensure that it comes off sparkling clean and professional. Having a strong checklist, diligent preparation before the source inspector’s visit and paying attention to fine details are key. Doing so will make it routine, and the feedback you get from the process will help to make your systems more profitable. To improve your preparation, FAI automation software along with high-performing CMM software will smooth your source buy-off. This modernization will pay for itself very quickly.
Embrace First Article Inspection
Some may see mandated first article inspection as burdensome and costly. But as part of their sub-contract requirements, they unenthusiastically comply. If we keep our eyes fixed on the benefits of FAI being excellence in process control, reduction in scrap, and superior customer satisfaction, we will see it as being completely worthwhile. Recognizing the peace of mind of knowing we contributed to the safety of our customers and the public, while ensuring there are minimized chances for supplier-customer disputes down the road, only adds to our comfort level. Here is a first article checklist that should be of help:
- Ensure all of the FAI requirements are clearly defined in the contract.
- Insist on specific and well-documented details of all the engineering characteristics that will need to be verified in the FAI report.
- Seek clarification for all digital product definition data and traceability requirements and make sure they are documented. Verify that there are no conflicts between DPD and physical engineering/contract definition and which is the contractual controlling authority.
- Prepare a comprehensive FAI plan before commencing. Make sure the applicable FAI specification (such as the AS9102) is in hand and compliance is an unmistakable part of the plan. It should be documented in your quality management system handbook.
- When any questions arise about what makes an acceptable product, or if manufacturing challenges arise during production, communicate with the customer and get them resolved (in writing) at the earliest opportunity. Make sure to convey to your organization that everyone is on the same team with the same goals in mind.
- Prepare for source inspection (if applicable) with reckless abandon like your life depends on it. You don’t want any friction with the source inspector, and a compliant, respectful collaboration is essential. If your in-house FAI source inspection representative isn’t a “people person,” hand the job off to someone else.
Happy first articles!
Author: Scott Knoche – Verisurf Software, Inc. (technical marketing & sales at Verisurf since 2002)
First Article Related Verisurf Videos:
VIDEO (click below)